The intricacies of crafting high-quality wheel felts remain an unsung hero in various industrial applications. Wheel felts, though perhaps less glamorous than other automotive or industrial components, play a pivotal role in maintaining the longevity and efficiency of machinery and vehicles. This article sheds light on the essential aspects of wheel felts, diving into their composition, applications, and the reasons why industries should invest in superior quality materials.
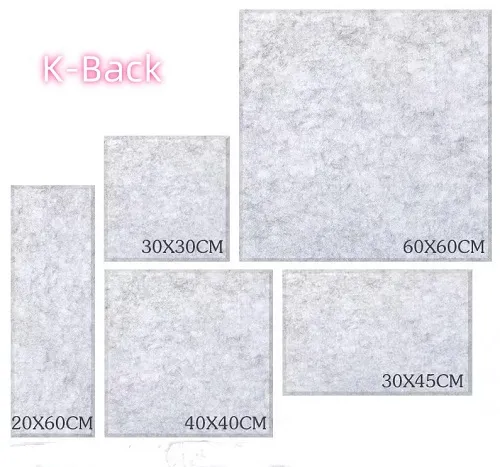
Wheel felts are commonly used in environments where there is a necessity for precise filtration, cushioning, or padding. Made from a variety of fibers, these felts are crafted through the process of matting, condensing, and pressing fibers together. The choice of fiber—from natural alternatives like wool to synthetic options like polyester or polypropylene—affects the felt's durability, flexibility, moisture resistance, and cost efficiency. This makes selecting the right type for a specific need a task that requires both expertise and experience.
Within automotive uses, wheel felts act as crucial silencers and protectors. They are embedded within the assemblies of brake systems, significantly reducing noise generated during friction between mechanical parts. Beyond noise reduction, these felts provide essential protection against dust and moisture, which can compromise the functionality of brake systems if allowed to accumulate unchecked. Experts in automotive engineering emphasize the importance of selecting high-density, moisture-resistant felts for these applications to ensure enhanced performance and extended lifespan of the braking system.
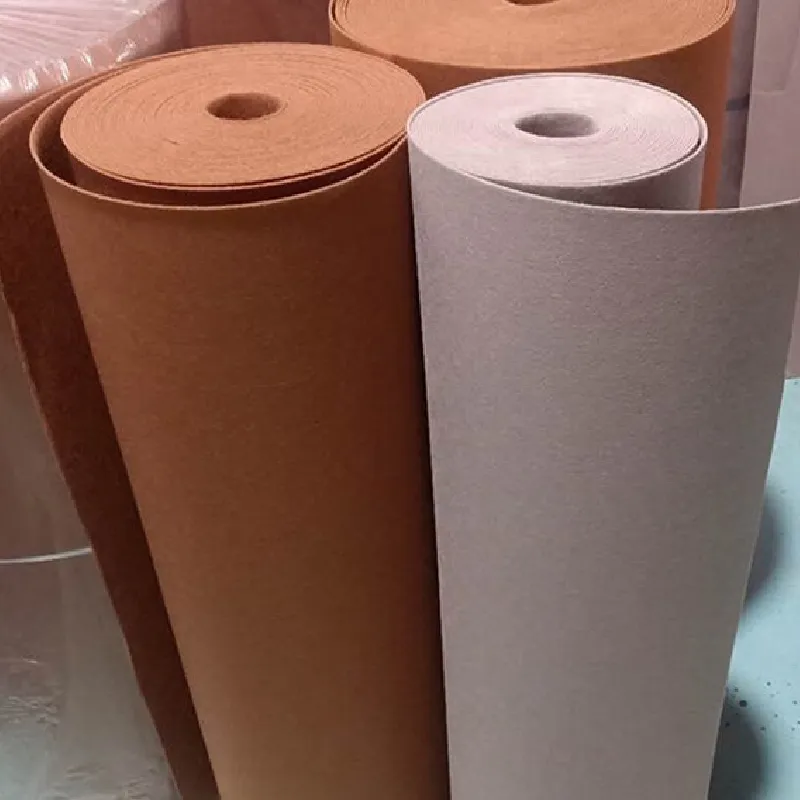
In industrial settings, the application broadens significantly. Wheel felts are integral in polishing operations, acting as buffers that delicately smooth surfaces while minimizing the risk of scratches. Their efficacy comes from their ability to adhere to polishing materials, distributing them evenly across surfaces for a consistent finish. For manufacturing experts, this uniformity is crucial, particularly in precision industries like aerospace and electronics where even minor imperfections can have significant ramifications. Consequently, trusted brands dedicated to quality control often choose high-grade wheel felts to streamline their operations, underlining the necessity for authoritative guidance in material selection.
Another less-discussed yet vital function of wheel felts is their role in sealing and gasketing. In environments prone to fluctuations in temperature and pressure, wheel felts provide reliable barriers, maintaining system integrity by preventing leaks and blocking contaminants. Engineers recommend using felt gaskets in places where vibration and expansion could otherwise weaken traditional seals.
The resilience and adaptability of felt make it a superior choice in many dynamic operating conditions.
wheel felt
The procurement of high-quality wheel felts boils down to their provenance and the expertise of their manufacturers. Companies with a robust history in textile engineering typically offer products subjected to stringent quality assurance processes. Purchasing from established manufacturers ensures that the products are tried and tested, reflecting the latest innovations in material science. Furthermore, credible manufacturers also provide comprehensive support, assisting businesses in selecting felts that precisely meet their application requirements, thus fostering trust with end-users.
Recognizing the environmental implications of industrial productions, leading companies are now pivoting towards sustainable manufacturing practices. Eco-friendly wheel felts crafted from recycled or biodegradable fibers align with the increasing consumer demand for responsible production. Industry leaders vouch for these sustainable alternatives, advocating for their effectiveness and underscoring the importance of resource conservation.
For industry professionals, the expertise in choosing the correct wheel felt is not merely about meeting current needs but also about anticipating future challenges. The continuous evolution in industrial techniques calls for wheel felts that can adapt to more rigorous demands. Leveraging the knowledge from experts across textile science, mechanical engineering, and environmental science can yield materials that push boundaries, setting the stage for innovations that redefine standard practices.
In conclusion, wheel felts are an essential, yet often overlooked, component in industrial and automotive applications. Their role in noise reduction, surface polishing, and system sealing is critical, necessitating the selection of high-quality materials backed by expertise and trusted supplier relationships. As materials science advances, the industry will continue to benefit from the evolution of wheel felts, ensuring improved performance, durability, and sustainability for the applications they serve.