Felt buffing polishing wheels are essential tools in achieving a perfect finish on a variety of surfaces, from metals to plastics and even ceramics. These wheels, crafted from compressed felt, are integral to the final stages of product manufacturing, helping professionals across numerous industries bring out the desired polish and sheen. As an expert in this field, I am well-versed in the nuances that determine the efficacy and quality of these essential tools.
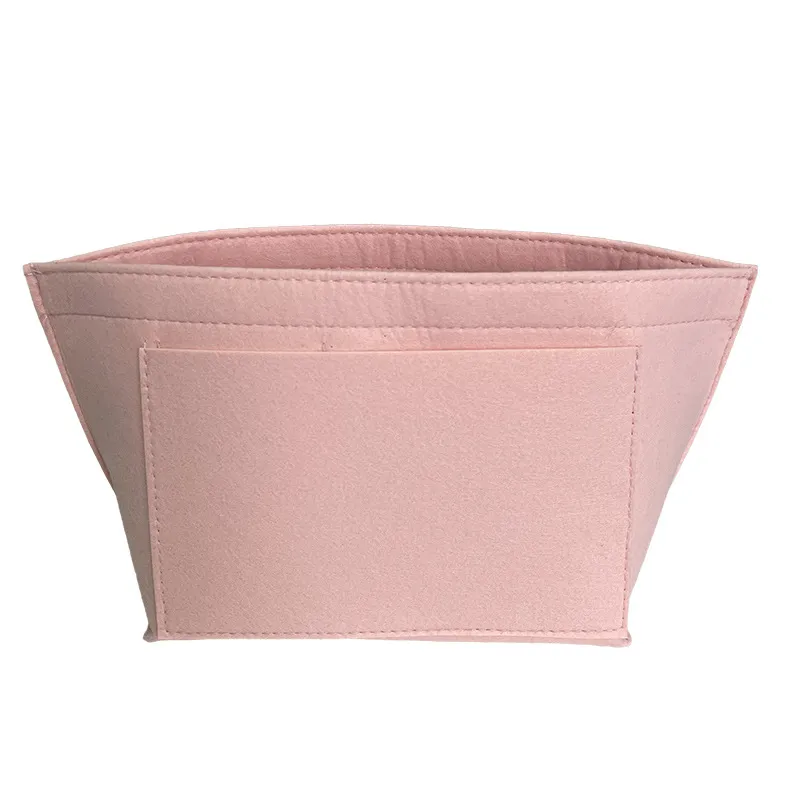
When selecting felt buffing polishing wheels, one must consider the density and thickness of the felt, as these attributes directly impact performance and outcomes. The density of felt is measured in grams per cubic meter (g/m³), and depending on the material and the degree of polish required, one should carefully select the appropriate density. For instance, hard felt wheels, with densities ranging from 0.48 to 0.56 g/m³, are excellent for aggressive polishing needs, while medium and soft densities, ranging from 0.40 to 0.46 g/m³, are more suitable for achieving a fine finish without removing too much material.
Versatility is another advantage of felt buffing polishing wheels, allowing them to be adapted to various shapes and sizes of workpieces. Custom cutting options are available, offering professionals the ability to tailor the wheel dimensions to fit specific requirements, thus maximizing efficiency and quality. Additionally, the flexibility of felt allows it to conform to the contours of a surface, which is particularly advantageous when working with intricate or curved designs.
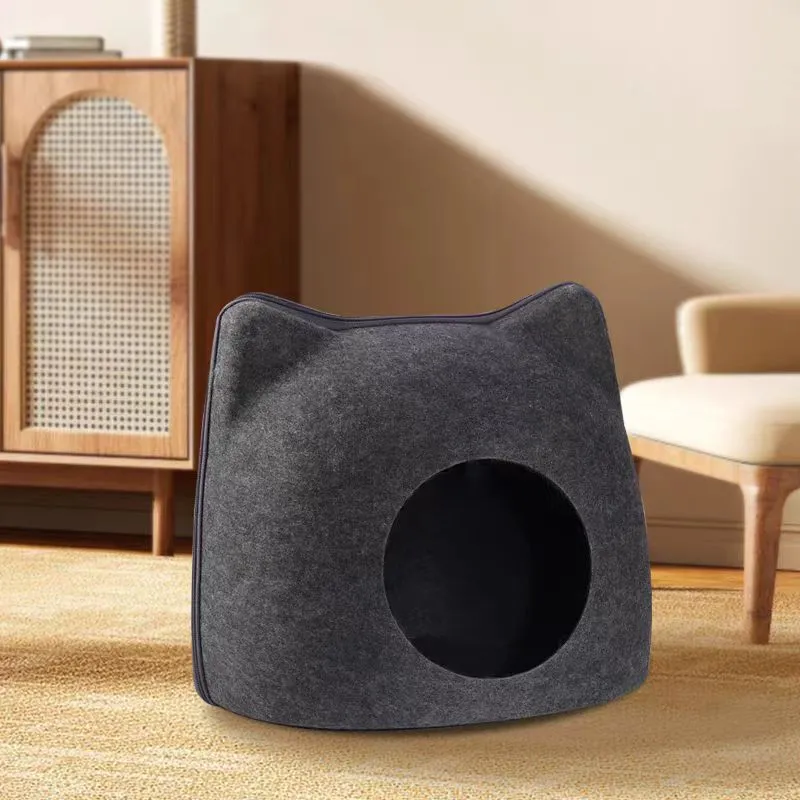
The choice of compound applied to the felt wheel significantly influences the polishing result. Polishing compounds range from coarse to fine, enabling users to address a broad spectrum of finishing needs—from removing scratches and minor surface imperfections to achieving a mirror-like gloss. It's advisable to choose these compounds based on the material being worked on; for instance, aluminum might need a different approach compared to stainless steel or brass.
One cannot overlook the importance of speed control in the polishing process. The rotational speed of the buffing wheel can dramatically affect the result—too slow, and the polishing might be ineffective; too fast, and there’s a risk of damaging the surface or burning the material. Generally, a safe starting point is around 3600 RPM for harder materials and can be lowered for softer surfaces or more delicate tasks. Professional operators should adjust speed according to the surface sensitivity and the desired finish.
felt buffing polishing wheels
Maintaining cleanliness of the felt buffing polishing wheels is crucial for ensuring longevity and consistent performance. Accumulation of polish residue and metal particles can adversely affect the efficiency of the wheel and the quality of the finish. Regular cleaning using a wheel rake or a similar tool is recommended to restore the felt’s texture and effectiveness. This practice not only prolongs the wheel’s life but also ensures that the workpieces continue to receive the highest quality finish.
It's wise to invest in high-quality felt buffing wheels from reputable manufacturers. Well-made wheels have undergone rigorous testing and quality control, ensuring they perform reliably and safely under various conditions. They also tend to provide consistent results, making them a favorite among tradespeople who rely on precision and durability.
Safety is paramount in any polishing operation. Protective eyewear, gloves, and appropriate work clothing are recommended, as polishing can generate heat and debris. Furthermore, ensuring your workspace is well-ventilated and free of hazardous materials is essential for creating a safe environment.
Through understanding the interplay of these variables—felt density, compound selection, rotational speed, and maintenance—professionals can master the use of felt buffing polishing wheels and achieve superior surface finishes. These wheels remain a testament to craftsmanship, embodying an intersection of tradition and modern manufacturing needs. Mastery in their use is not just about acquiring tools but about developing a deep appreciation of material science and precision engineering techniques that define the modern era of manufacturing and production.