Automotive felt is rapidly gaining traction as an essential component in the automotive industry, valued for its versatility and performance excellence. As an expert in automotive materials with years of direct industry involvement, the intricate qualities and applications of automotive felt deserve detailed exploration.
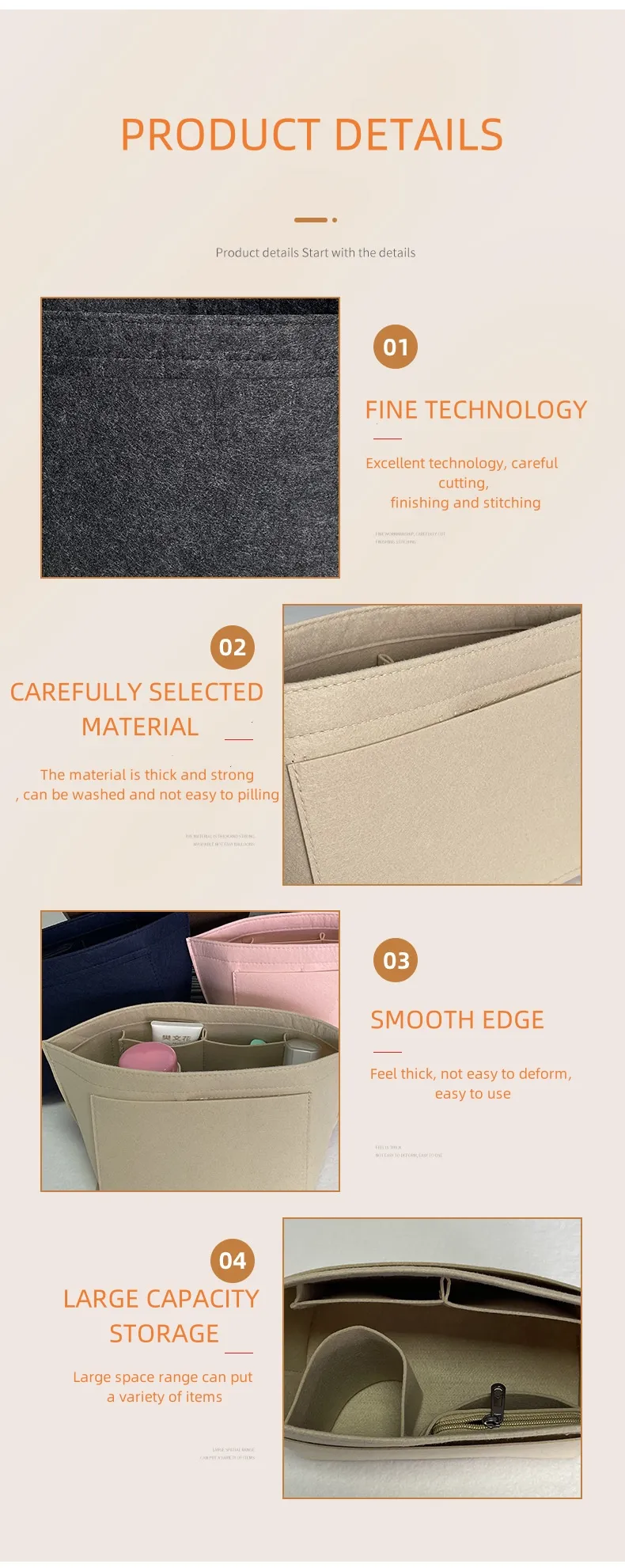
Automotive felt, traditionally overshadowed by synthetic counterparts, stands out due to its natural origin and adaptability to various automotive functions. This material is often made from wool or a blend of natural and synthetic fibers, which provides a unique combination of softness, durability, and acoustic insulation — qualities highly sought after in automotive manufacturing.
One of the foremost applications of automotive felt is in sound insulation. Vehicle cabins are increasingly seen as sanctuaries of peace amidst bustling urban environments, and effective soundproofing is crucial. Felt's dense fiber matrix is exceptional at dampening noise vibrations, ensuring a quieter ride irrespective of the external environment. As exhaust and engine sounds are muffled, passengers remain undisturbed, appreciating a more refined driving experience.
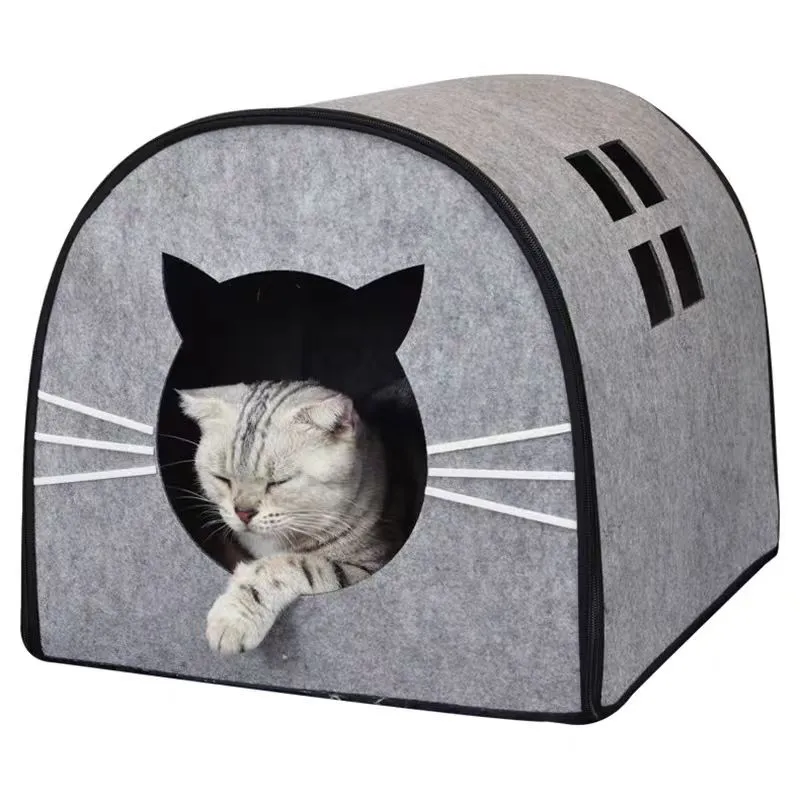
The material's innate resilience and flexibility contribute significantly to vibration damping.
In automotive environments where multiple moving parts can create vibrational disturbances, felt buffers these dynamics efficiently. Its natural elasticity helps in absorbing and dissipating vibrations, reducing wear and tear on components and prolonging their lifespan. This not only enhances vehicle performance but also aids in minimizing maintenance costs over time.
Beyond its acoustic benefits, automotive felt plays a vital role in thermal management. With increasing emphasis on energy efficiency and climate control within vehicles, managing thermal flux becomes paramount. Felt is used extensively as a lining material in door trims, dashboards, and undercarriages, offering thermal resistance and thus contributing significantly to maintaining optimal cabin temperatures with lower energy consumption.
automotive felt
Additionally, in the context of sustainability, automotive felt represents an eco-friendly option. Wool, being a biodegradable and renewable resource, appeals to manufacturers aiming to reduce their environmental footprint. The focus on sustainable manufacturing practices has become more pronounced as the automotive industry grapples with the sustainability challenge. By integrating felt, manufacturers can meet consumer demand for greener alternatives without compromising on quality or performance.
The expertise entrenched in producing high-quality automotive felt also speaks to its authority in the industry. Leading manufacturers adhere to stringent quality control processes, ensuring that their felt products meet the rigorous demands of automotive standards. The synthesis of tradition and innovation in felt production showcases the commitment to delivering reliable, high-performance materials.
Despite the prevalence of synthetic substitutes, the trustworthiness of automotive felt is maintained through consistent performance outcomes. The assurance of quality comes from established testing protocols and certifications that these products undergo, often surpassing the performance benchmarks that purely synthetic materials fail to match. Testimonials from industry professionals underscore its value, further anchoring its credibility.
In summary, automotive felt is not merely a material choice but a strategic component in automotive manufacturing. Its ability to enhance acoustic comfort, provide thermal management, and offer sustainable solutions underscores its indispensability. For manufacturers seeking a combination of performance, cost efficiency, and eco-friendliness, automotive felt stands as a benchmark, reaffirming its place in the future of automotive innovations. Leveraging such materials reflects commitment to cutting-edge automotive engineering while resonating with contemporary societal values of sustainability and quality.